
..................................................................................................................................................
Typical Road
Structure Details
By: Haseeb Jamal
Composition of Road
Structure:
Road Structure Cross Section is
composed of the following components:
1.
Surface/Wearing Course
2.
Base Course
3.
Sub Base
4.
Sub Grade
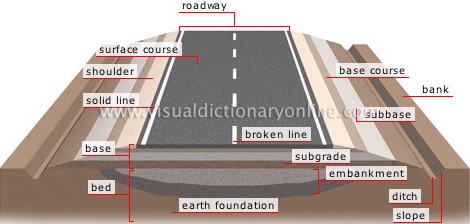
1.
Surface/Wearing Course in pavement cross section:
The top layers of pavement which is
in direct contact with the wheel of the vehicle. Usually constructed of
material in which bitumen is used as binder materials.
a. Bituminous
Pavement:
Consists of combination of mineral
aggregate with bituminous binder ranging from inexpensive surface treatment ¼
in or less thick to asphaltic concrete.
For good service throughout the full
life bituminous pavement must retain following qualities.
· Freedom from cracking or raveling.
· Resistance to weather including the effect of surface water heat
and cold.
· Resistance to internal moisture, particularly to water vapors.
· Tight impermeable surface or porous surface (if either is needed
for contained stability of underlying base or subgrade).
· Smooth riding and non-skidding surface.
The design should be done so that to
meet the above requirements for considerable number of years (need proper design
and construction supervision).
Pavement meeting all the requirements
above have been product if six distinctly different construction processes as
follows:
· Heat a viscous bituminous binder to make it fluid, then in a
plant mix it with heated aggregate place and compact the mixture while it is
hot.
· Use fluid bituminous binder, mix it with aggregate at normal
temperature. Mixing may be done at a plant (plant mix) or on the prepared
roadway base (road mix). Spread and compact the mixture at normal temperature.
· Add solvent such as naphtha or kerosene to a viscous bituminous
binder to make it fluid with aggregate at normal temperature by either plant or
road mix methods. Spread and compact at normal temperature before solvent
evaporates.
· Use fluid emulsion of viscose bituminous binder in water, mix it
with aggregate at normal temperature by either plant or road mix method. Spread
and compact at normal temperature before the emulsion breaks down with its
components.
· Spread and compact clean crushed aggregate as for water bound
macadam. Over it spray heated dissolved or emulsified bituminous binder which
penetrates open areas of the rock and binds the aggregate together. Thus is
commonly called “Penetration Method”.
· Spread bituminous binder over the roadway surface then cover it
with properly selected aggregate. This is commonly called the “Inverted
Penetration Method”.
Selections based on the requirements
and economy, large volume of heavy vehicles, low traffic volume etc.
2. Base course
It is the layer immediately under the
wearing surface (Applies whether the wearing surface is bituminous or cement
concrete and or more inch thick or is but a thin bituminous layer).
As base course lies close under the
pavement surface it is subjected to severe loading.
The material in a base course must be
of extremely high quality and its construction must be done carefully.
1. Granular Base
Course
2. Macadam Base
3. In-water bound
Macadam
4. Treated Bases
3. Sub Base:
It is layer of granular material
provided above subgrade generally natural gravel. It is usually not provided on
subgrade of good quality. It is also called granular subbase.
a. Function of
Sub base in Road Cross Section
· It enables traffic stresses to be reduced to acceptable levels
in sub-grade in the Road Cross Section so that excessive deformation is
prevented.
· It acts as a working plate form for the construction of upper
pavement layers.
· Acts as a drainage layer, by protecting the sub grade from
wetting up.
· It intercept upward movement of water by capillary action.
· It acts as a separating layer b/w subgrade and road base. By
this it prevent the two layers from mixing up.
b.
Characteristics of materials used in Sub Base:
The subgrade material should be clean
and free from organic matter and should be able to be compacted by roller, to
form stable sub-base. The material should have following characteristic.
· Well graded uniformity coefficient (D60/D10) should not be less
than 3.
· Fraction passing sieve #200 shall not be greater than 2/3rd of
the fraction passing sieve #40.
· Should have a L.L not greater than 25%.
· P.I not greater than 6
· CBR should not be less than 25.
See also: CBR Test Procedure

· In coarse grain, aggregate retained by #10 sieve, %age of wear
shall not be greater than 5%.
· The max dia of any particle shall not be greater than 2/3ed of
the layer thickness of sub-base.
- Typical
particle size distribution for the sub-base (granular) when will meet
strength requirement are:
B.S Sieve Size
|
% By mass of total Aggr. passing test sieve
|
50
|
100
|
37.5
|
80 - 100
|
20
|
60 - 100
|
5
|
30 - 100
|
1.15
|
170 - 75
|
0.3
|
9 - 50
|
0075
|
5 - 25
|
* To avoid
intrusion of silt and clay material in sub-base from subgrade
D15 (sub base) < 5 D15
(sub grade)
- Recommended
plasticity characteristic for granular Sub Base (Road Note 31) are;
Climate
|
Liquid Limit (L.L)
|
Plasticity Index (P.I)
|
Moist or wet tropical
|
< 35
|
< 6
|
Seasonal wet tropical
|
< 45
|
< 12
|
Arid & Semi Arid
|
< 55
|
< 20
|
4. Sub Grade:
Consists of the
naturally occurring material on which the road is built, or the imported fill
material used to create an embankment on which the road pavement is
constructed.
Subgrades are also considered layers
in the pavement design, with their thickness assumed to be infinite and their
material characteristics assumed to be unchanged or unmodified.
Prepared subgrade is typically the
top 12 inches of subgrade.
Haseeb
Jamal.
I am a Civil Engineer, graduated from University
of Engineering and Technology, Peshawar, Pakistan in 2010. I also
have a PG-Diploma in Disaster Management and
MS in Urban
Infrastructure Engineering (In Progress). My expertise include civil
related softwares like AutoCAD,
SAP2000, MS Project, Primavera, MS Office and GIS. My technical skills include
project management, monitoring and evaluation, structural assessment, disaster risk
management, Quantity survey, land survey, material testing, site management and
technical writing. I am trained in writing project progress reports as well as
proposals and concept papers. I have also received advanced training on
surveying, proposal writing, Monitoring and Evaluation of projects as well as
organizations.
I
have worked as Project Engineer at National Research and Development
Foundation, Peshawar and CENCON Associates. I also worked with Spectra
Engineering Solutions as Senior Civil Engineer in monitoring of World
Bank and UNDP funded projects all over Khyber Pakhtunkhwa and FATA. Currently,
I am working as Deputy Manager Development at NayaTel, Peshawar.

No comments:
Post a Comment