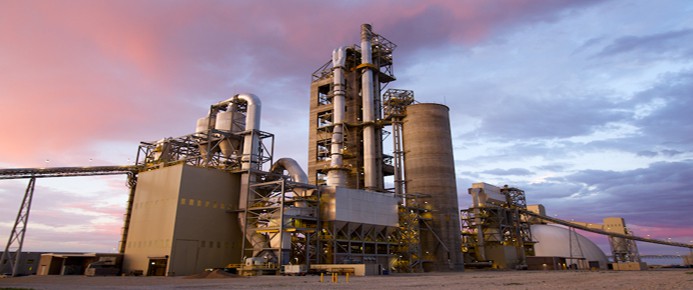
..................................................................................................................................................
How
to Make Portland Cement: The Full Manufacturing Process
by
shahe
Portland cement is the most common type of
cement.
In particular, “Ordinary Portland cement” is
the normal, grey cement with which most people are familiar.
Material made by heating a mixture of
limestone and clay in a kiln at about 1400 to 1600 degrees (2550 to 2990 F),
then grinding to a fine powder with small addition of gypsum.
How to Make Portland Cement
Raw materials for modern cement making:
Limestones
argillaceous shales
Chalks
schists
Shells
clays
calcareous nodules
other iron-bearing aluminum-silicates.
Raw Materials Preparation
Cement is typically made from limestone and
clay or shale and sand. These raw materials are extracted from the quarry,
crushed to a very fine powder and then blended in the correct proportions.
Summary of Manufacturing process
Cement is typically made from limestone and
clay or shale. These raw materials are extracted from the quarry to a very fine
powder in correct proportions.
These blended raw materials are called the
“raw feed” or “kiln feed” and is heated in a rotary kiln where it reaches a
temperature of about 1400 c t0 1500 c.
In its simplest from, the rotary kiln is a
tube up to 200 meters long and perhaps 6 meters in diameter, with a long flame
at one end.
The raw feed enters the kiln at the cool and
end gradually passes down to the hot end, then falls out of the kiln and the
cool downs.
The material formed in the kiln is described
as “clinker” and is typically composed of rounded nodules between 1 mm and 25
mm across.
After cooling, the clinker may be stroked
temporarily in a clinker store, or it may pass directly to the cement mill.
The cement mill grinds the clinker to fine
powder.
A small amount of gypsum – a form of calcium
sulfate is normally ground up with the clinker.
The gypsum controls the setting properties of
the cement when water is added.
Cement manufacturing process in details
Raw materials: The main raw materials used in
the cement manufacturing process are limestone, sands, shale, clay and iron
ore.
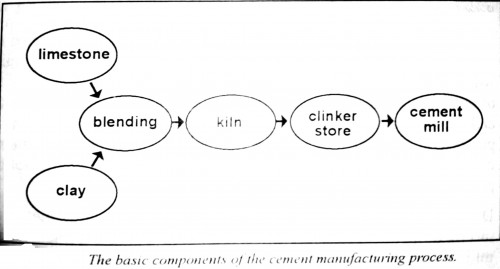
Another source of raw materials industrialist
by-products.
Raw Material preparation: Mining of limestone
requires the use of drilling and blasting techniques.
The blasting techniques use the latest
technology to insure vibration, dust, and noise emissions are kept at a
minimum.
Blasting produces materials in a wide range
of size from approximately 1.5 meters in diameter. Through a series of the
crushes and screens, the limestone is reduced to a size less than 100 mm and
stored until required.
Depending on size, the minor materials may or
may not be crushed before being stored in separated areas until required.
Raw Grinding
Wet process: in the wet process, each raw
material is proportioned to meet a desire chemical composition and feed to a
rotating ball mill with water.
The raw materials are ground to a size where
the majority of the materials are less than 75 microns. Materials exciting the
mill are called “slurry” and have flow ability character.
Following the homogenization process, the
slurry is stored in tanks until required.
Dry process: In the dry process, each raw
material is proportioned to meet a desired chemical composition and fed to
either a rotating ball mill or vertical roller mill.
The raw materials are dried with waste
process gases and ground to size where the majority of the materials are less
then 75 microns.
The dry materials exciting either type of
mill is called “kiln feed”.
Pyroprocessing
Whether the process is wet or dry, the same
chemical reaction take place.
Basic chemical reaction are: evaporating all
moisture, calcining the limestone to produced free calcium oxide with the minor
materials.
This results in a fine black, nodular product
known as “clinker” which has the diverse hydraulic properties.
Wet process
In the wet process, the slurry is fed to a
rotary kiln, which can be from 3.0 m to 5.0 m in diameter and from 120.0 m to
165.0 m in length.
The rotary kiln is made of steel and lined
with special refractory materials to protect it from the high posses
temperature.
Posses temperature can reach as high as 1450
C during the clinker making process.
Dry Process
In the dry process, kiln feed is to a preheat
tower, which can be as high as 150.0 meters.
Materials from the preheated tower is
discharged to a rotary kiln with can have the same diameter as a wet posses
kiln but the length is much shorter at approximately 45.0 m.
The preheated tower and rotary kiln are made
of steel and lined with special refractory materials to protect it from the
high process temperature.
Regardless of the process, the rotary kiln is
fired with an intense flame, produced by burning coal, cock, oil, gas, or waste
fuels.
Welcome
to Civil Engineers Forum. Civil Engineering
is interesting and fun if it is treated properly. Civil Engineers Forum was
founded to provide all necessary civil engineering basic knowledge as well as
to gather important references on civil engineering in one place so that every
civil engineering student, as well as professional civil engineers, can be
benefited.
Within
a short time, the website became popular among CE niche and now its one of the
best site for professional civil engineers & civil engineering students and
has a vast collection of unique civil engineering niche related articles,
research paper, knowledge center, case study, software, spreadsheets, books,
designs, presentations etc. Write & share your experience in civil
engineering topics to help other civil engineers & civil engineering
students.
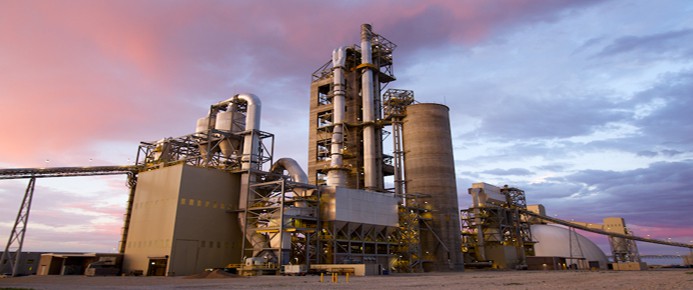
No comments:
Post a Comment