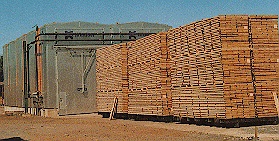
..........................................................................................................................................................
By: Haseeb Jamal
Artificial (kiln) Seasoning
Artificial
methods of seasoning timber
Kiln
drying of lumber is perhaps the most effective and economical method available.
Drying rates in a kiln can be carefully controlled and defect losses reduced to
a minimum. Length of drying time is also greatly reduced and is predictable so
that dry lumber inventories can often be reduced. Where staining is a problem,
kiln drying is often the only reasonable method that can be used unless
chemical dips are employed.
Kilns
are usually divided into two classes:
1.
Progressive
2.
Compartment
Both
methods rely on the controlled environment to dry out the timber and require
the following factors:
· Forced air circulation by using large fans, blowers,
etc.
· Heat of some form provided by piped steam.
· Humidity control provided by steam jets.
Amount
and Duration of Air, Heat and Humidity depends upon:
1.
Species
2.
Size
3.
Quantity
1. Progressive
Seasoning:
In
the progressive kiln, timber enters at one end and moves progressively through
the kiln much as a car moves through a tunnel.
Temperature
and humidity differentials are maintained throughout the length of the kiln so
that the lumber charge is progressively dried as it moves from one end to the
other.
Progressive
kilns may be further subdivided into natural draft kilns in which heated air is
allowed to rise through the material by natural convection, and forced draft
kilns in which fans are employed to force the air through the wood.
A
progressive kiln has the stack on trolleys that ‘progressively’ travel through
chambers that change the conditions as it travels through the varying
atmospheres.
Progressive Kiln
The
advantage of this system, although
much larger, has a continuous flow of seasoned timber coming off line.
A
number of commercial processes for seasoning of timber are available, the most
common of which is kiln-drying.
Kiln
seasoning accelerates the process of seasoning by using external energy to
drive the moisture out.
The
timber is stacked in much the same way as it is for air drying, and is placed
inside a chamber in which the conditions can be varied to give best seasoning
results.
Air
is circulated around the charge (stacked timber) and the temperature and
humidity can be varied to give optimum drying.
Each
species has different cell characteristics and therefore requires different
drying schedules.
Typically,
the timber may be in the kiln for a period of between two days to one week.
Generally,
it is not feasible to kiln-dry structural timber in thicknesses greater than 45
mm, although there are limited amounts of 70 mm thick kiln-dried softwood
members in the market place.
All
untreated structural pine and some commercial hardwoods are seasoned, mostly
using kilns that are often heated by sawmill by-products or gas.
Plenty
of research is continually being done to determine kiln drying schedules for
different species.
An
optimum schedule will remove the moisture as quickly as possible, with the
minimum quantity of introduced energy, and giving minimum damage to the dried
timber.
After
kiln seasoning, there is often some damage to cells near the surface of the
wood. (All of the moisture passes through those cells.)
They
have in fact collapsed, but can easily be ‘pumped back up’ in a reconditioning
chamber. This chamber introduces steam for a period and puts some moisture back
into the outer cells and removes the effect of seasoning collapse.
Hard
woods have closed cell structure, so take more time in being seasoned and
dried.
Conventional
kiln-drying for hardwoods uses temperatures well below the boiling point of
water. This avoids damage to the wood
fibres which, if the seasoning is not properly controlled, can experience loss
of strength.
In
seasoning hardwoods, the process is slow and can be economically undertaken by
first of all air-drying or partially seasoned for a period which can be
anywhere from 3 to 9 months, depending upon the thickness of material, the
ambient temperature and humidity and the species.
The
partial seasoning process can be accelerated for some hardwoods by using
fan-forced pre-drying in a controlled (but not kiln) environment, to reduce the
lead time for kiln-drying to 20 to 30 days.
Once
the sawn hardwood material reaches fibre saturation point or slightly below (at
a moisture content of about 20% to 25%), it is then placed in kilns usually for
up to 10 - 14 days (depending upon the thickness of the sawn timber) in order
to bring the moisture content down to between 10% and 15%.
This
drying process must be strictly controlled and monitored in order to avoid
drying degrade.
..
..
The
amount and duration of air, heat and humidity again depends on species, size,
quantity, etc.
2. Compartmental
Seasoning:
A
compartment kiln is a single enclosed container or building, etc.
The
timber is stacked as described above and the whole stack is seasoned using a
programme of settings until the whole stack is reduced to the MC required.
Compartment
kilns differ from progressive kilns in that the timber is loaded into the kiln
and remains in place throughout the drying process.
Compartment
kilns are usually smaller than progressive kilns, and because of their
construction the temperature and humidity conditions within them can be closely
controlled.
Consequently,
they are often used to dry expensive material or woods which are difficult to
dry.
Circulation
may be either forced or natural just as with progressive kilns. Drying
conditions cannot be controlled as closely in natural draft compartment kilns,
however, as in forced draft kilns, and the rate of drying is also slower.
For
these reasons kilns built today are of the forced draft type and many of the
old natural draft types have been converted.
Haseeb Jamal. I am a Civil Engineer, graduated from University
of Engineering and Technology, Peshawar, Pakistan in 2010. I also
have a PG-Diploma in Disaster Management and
MS in Urban
Infrastructure Engineering (In Progress). My expertise include civil
related softwares like AutoCAD,
SAP2000, MS Project, Primavera, MS Office and GIS. My technical skills include
project management, monitoring and evaluation, structural assessment, disaster
risk management, Quantity survey, land survey, material testing, site
management and technical writing. I am trained in writing project progress
reports as well as proposals and concept papers. I have also received advanced
training on surveying, proposal writing, Monitoring and Evaluation of projects
as well as organizations.
I have worked as Project
Engineer at National Research and Development Foundation, Peshawar and
CENCON Associates. I also worked with Spectra Engineering Solutions as Senior
Civil Engineer in monitoring of World Bank and UNDP funded projects all
over Khyber Pakhtunkhwa and FATA. Currently, I am working as Deputy
Manager Development at NayaTel, Peshawar.

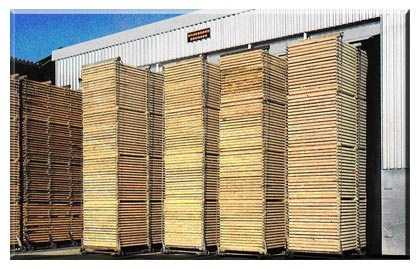
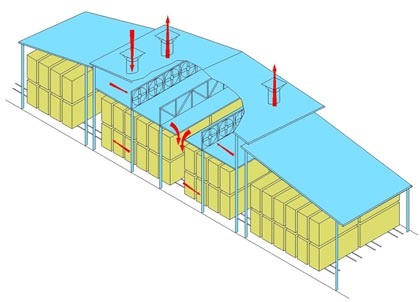
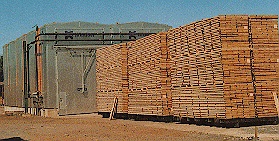
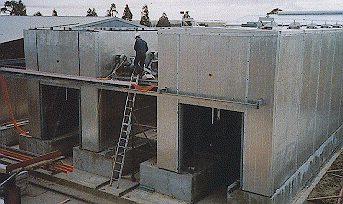
No comments:
Post a Comment