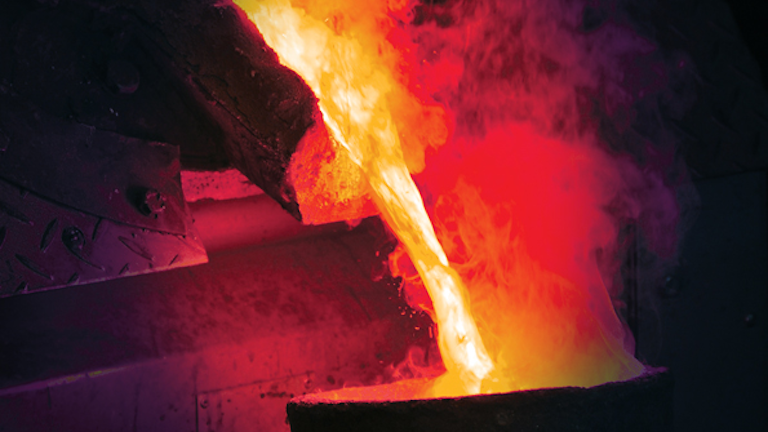
...........................................................................................................................................................
What’s the Difference Between Cast and
Wrought Iron?
Brad
Done
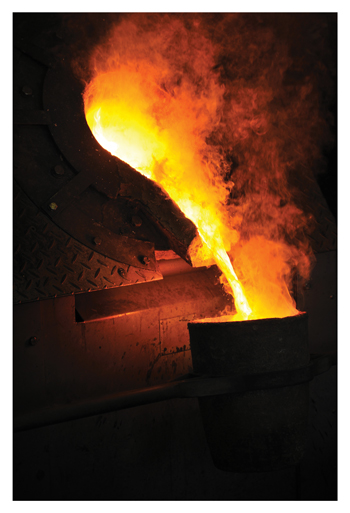
Cast iron is iron that has been melted, poured into a mold, and
allowed to cool.
Wrought iron is iron that has been heated and then worked with tools.
In fact, the term “wrought” derived from the past participle of the word
“worked.”
But let’s dig into the details.
Cast Iron
“Cast iron” is a generic term
that refers to a range of iron alloys, but is typically associated with the
most common, gray iron.
While cast iron may sound like
the cast form of pure iron, it's actually an alloy containing 2 to 4% carbon,
plus smaller amounts of silicon and manganese.
Other impurities, such as
sulfur and phosphorus, are also common.
Cast
iron is formed by smelting iron ore, or melting pig iron (the product of iron
ore extraction), and mixing with scrap metals and other alloys.
The liquid mixture is poured
into molds and allowed to cool and solidify.
Due to its higher carbon
content, cast iron solidifies as a heterogeneous alloy, so it contains several
materials in different phases within its microstructure, which affects its
physical properties.
For example, cast iron has
carbon particles within its microstructure which form elongated graphite flakes
when the metal cools.
Graphite is low in density and
hardness but high in lubricity. So, it offers little in terms of structural
advantage, but it does compromise the surrounding iron.
Compared to wrought iron or
steel, cast iron is brittle, hard, and non-malleable. It can’t be bent,
stretched, or hammered into shape.
Its weak tensile strength means
that it will fracture before it bends or distorts.
It does, however, have good
compression strength, and was used prominently in building construction before
the advent of the steel industry in the early 20th Century.
Compared to steel, cast iron has a lower
melting point, and is more fluid and less reactive with mold materials, making
it well-suited for casting.
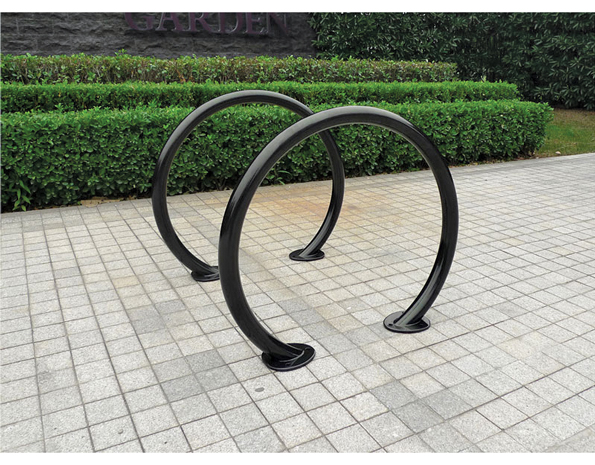
Cast iron has largely been replaced by steel
in the construction industry, but it is still used for many industrial
applications.
Wrought iron is often characterized by its
fibrous appearance, but it’s also softer and more ductile than cast iron.
Wrought iron is highly malleable, meaning it
can be heated, and re-heated, and worked into various shapes.
In fact, it gets stronger the more it’s
worked.
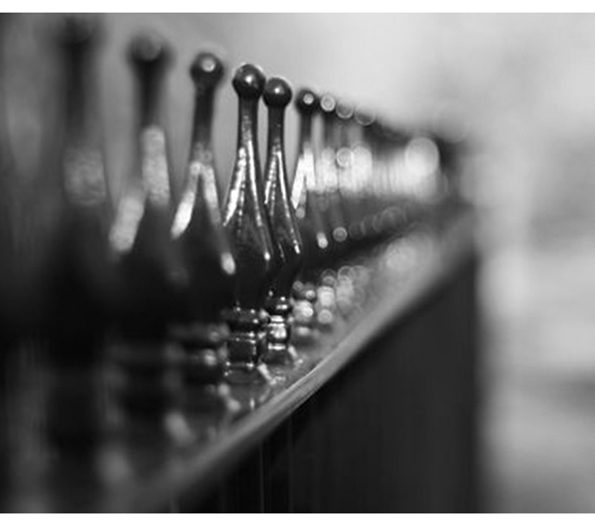
In general, it strongly resists fatigue. It
deforms without failing unless overloaded well beyond capacity or distorted
from exposure to intense heat (e.g.., from fire).
It was widely used throughout the 19th Century
in building construction, but was replaced by steel in the 20th Century.
Today, wrought iron is used primarily for
decorative applications.
Corrosion
Cast and wrought iron are both susceptible to
corrosion when bare surfaces are exposed to oxygen in the presence of moisture.
Unlike other metals that form a protective
oxidative coating, iron will — given enough time — rust and flake away
entirely.
This can be challenging for outdoor
environments where exposure to precipitation and humidity can be ongoing.
To prevent rust, iron products should be
coated to prevent exposure. Paint is commonly used to protect bare metal.
Powder coatings are another method and
well-suited for outdoor furnishings susceptible to wear in high-traffic areas.
Powder coatings are highly durable and won’t
fade, chip, or crack over extended periods of time.
Brad Done, Vice President
Reliance Foundry Co. Ltd., British Columbia, Canada
Reliance Foundry Co. Ltd., British Columbia, Canada
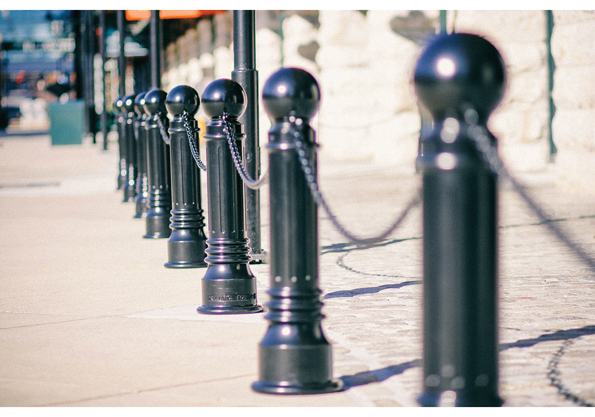
No comments:
Post a Comment